Custom Chemicals International (CCI) is a manufacturer based in the North of Brisbane, they have a 32-year history as a small factory producing high-quality commercial cleaning products and have more recently expanded with the ability to produce specialty products and now have the capacity to produce large volume contract packing.
With growth comes new equipment and bigger premises and with that the requirement to maintain the space vigilantly. Some of the plant and equipment had been installed for some time which as you might expect, means that upgrades and replacements need to take place.
CCI had been experiencing a number of critical breakdowns that were causing bottlenecks in production, specifically on their conveyor line. Sometimes the conveyor would breakdown on a daily basis. They had asked various electrical contractors to help work out what the problem was but with no luck. Enter Jason and the QMS Electrical team and a new insightful way of seeing the problem and to CCI’s delight – the problem was solved. It turned out that the main drive was on its way out and some wiring needed to be replaced. Dean Hoey from CCI stated that,
“it was such a relief to get the conveyor line sorted, we had engaged the services of multiple electrical contractors, all of whom could not fix the problem entirely. Jason and his team are different from other electrical contractors, they think differently, they explain what they are doing and are patient with us. Now we wouldn’t ask any other electricians to manage our systems, in fact, I have his number of speed dial”.
Another instance of QMS coming to the rescue happened when CCI had a speed controller issue, they couldn’t source a new line from anywhere which was really debilitating production. Dean called QMS and Jason turned up himself (that day and out of hours) to fix the controller. He had sourced the new line, collected it and then rushed over to install it. “After I left for the day Jason stayed on to complete the job. The operations team were there to lock up but Jason was left to his own devices to get it all fixed, which he did. Jason and his team are very trustworthy. I knew that when I got to work in the morning everything would be working and ship shape again”.
“Choosing QMS Electrical is a no brainer if you want an innovative, forward-thinking, conscientious electrician who will go to the ends of the earth to help you fix your problems, then call Jason and his team. They get here within the hour, with all the right equipment and supplies and we know they will get the job done, I highly recommend them and refer them constantly to other companies”.
QMS Electrical has an ongoing maintenance schedule with CCI which means that we work with CCI and the operations team so we know what needs to be replaced or updated and when. This means that they experience fewer breakdowns and that faults in the equipment are simple to fix because we are intrinsically involved with the running of the conveyors and systems they use. We give our clients a heads up if we think that there is something that needs attention before the point of no return – this often saves them time and money in the long run.
QMS have performed their electrical maintenance and upgrades since Jan 2017.
Being on a schedule maintenance contract means that we will service all electrical and lighting circuits, replace circuit breakers, relays and contactor’s, motors, motor drives (as well as things like intelligent motor starters/controllers). We also service and test all emergency stops & RCD’s. We carry out regular test & tag procedures and are on call for any and all emergency/breakdown callouts.
We really enjoy working with the team at CCI, the respect flows both ways.
Provided services:
Emergency and Breakdown call outs
Scheduled maintenance
Upgrade wiring and electrics
Replace circuit breakers
Service motors /controllers/ drives
Problem solving
Test n tag
RCD tests
Emergency stop tests
Great customer service
Trust
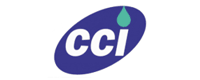